Illumination Works (ILW) recently conducted a live webinar featuring industrial internet of things (IIoT).
The focus was our recent Innovation Lab project leveraging PTC ThingWorx to ensure environmental safety and correct air and water conditions/quality during depaint, paint, and cure of aircraft and aircfraft parts inside large hangar bays.
We sat down with Stefan Salzmann, ILW IoT Digital Designer/Developer, to take a deep dive into the interesting aspects of this project.
Tell us about the use case for the paint hangar.
The use case was targeted to the requirements of a manager of a paint hangar with the purpose of repainting military aircraft. In our use case, there are seven individual bays and each bay is capable of housing and painting an entire aircraft.
Once a plane enters the facility, it goes into the preparation phase. In this stage, the plane is sanded down to its bare metal, or a solvent is applied to strip the old layer of paint. Once the plane is properly stripped, it enters the painting phase where the plane is painted using spray painting guns that allow the paint to be very lightweight. The spray painting guns use a zinc chromate-based paint, which includes environmentally hazardous chemicals that reach large amounts. The manager of the paint hangar monitors those properties closely to ensure the safety of both the airmen and the plane.
Once the plane is painted, it can begin drying in what is known as the cure phase. The cure phase takes one day to a whole week to complete. During this time, the same hazardous chemicals from the paint phase must continue to be monitored and closely measured to make sure the chemicals lingering around the hangar are dissipating in a timely manner. Once the plane is certified and completed for the job, it enters back into service and begins flying again.
To ensure our use case and the dashboard we created was accurate and relevant to our client, we sought information from Air Force subject matter experts to identify edits to the dashboard depending on what they thought would be the most useful. This process was iterated every couple of weeks to confirm everyone was up to date on the design and the clients were able to give feedback that would best assist them in their use case.
Join our mailing list like hundreds of other like-minded technology lovers!
What were the goals for the Paint Hangar Analytic Dashboard?
The initial goal was to present the Air Force with a dashboard that allows Airmen and civilians to monitor properties within their paint hangar. The next goal was to take simulated data and put that into ThingWorx to build an easy-to-use and interactive user interface around that data. The last goal was to have simulated data that represents real-life sensors used by the Air Force in a paint hangar scenario and present it in the user interface. Throughout the effort, we met with Air Force subject matter experts to ensure the data points were realistic.
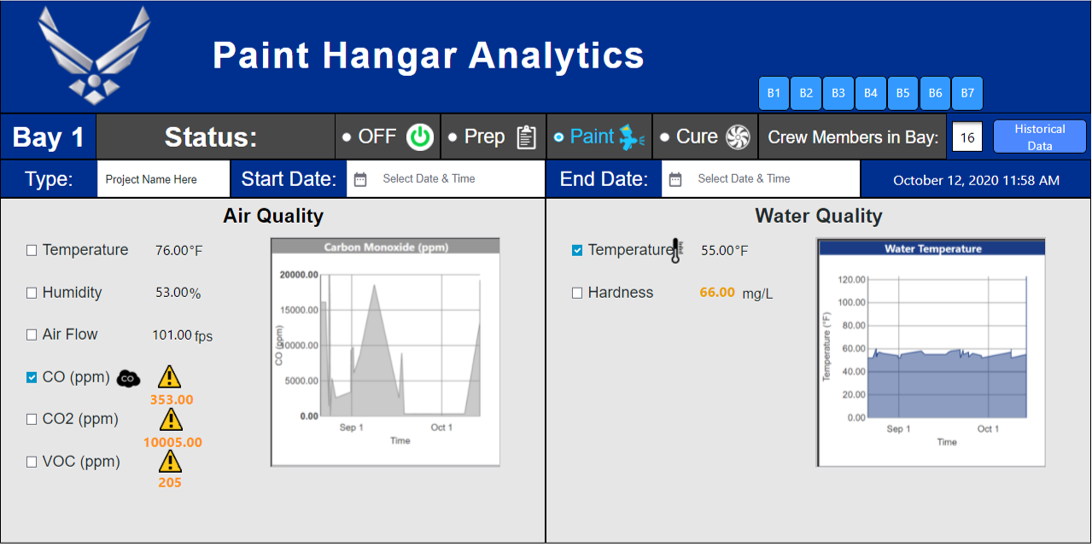
Can you talk to the business value of IoT monitoring in a paint hangar?
First and foremost, we want to maintain a safe environment for the workers. In terms of business value, its greatest value is its contribution to keeping the operation running in an optimal way by making sure you have the right temperature, humidity, water levels, and characteristics. Also, if something does go wrong, you want to be able to identify environmental issues as they occur to avoid shutdowns and rework, saving both time and money.
The advantages of using an Industrial IoT platform such as ThingWorx is that is supports business goals in terms of maximizing revenue, reducing costs, and increasing efficiency. In our specific paint hangar use case, we focus on increasing throughput, increasing service levels, reducing labor costs, providing easy-access data, providing a safe and compliant environment, and improving the efficiency of the paint hangars themselves.
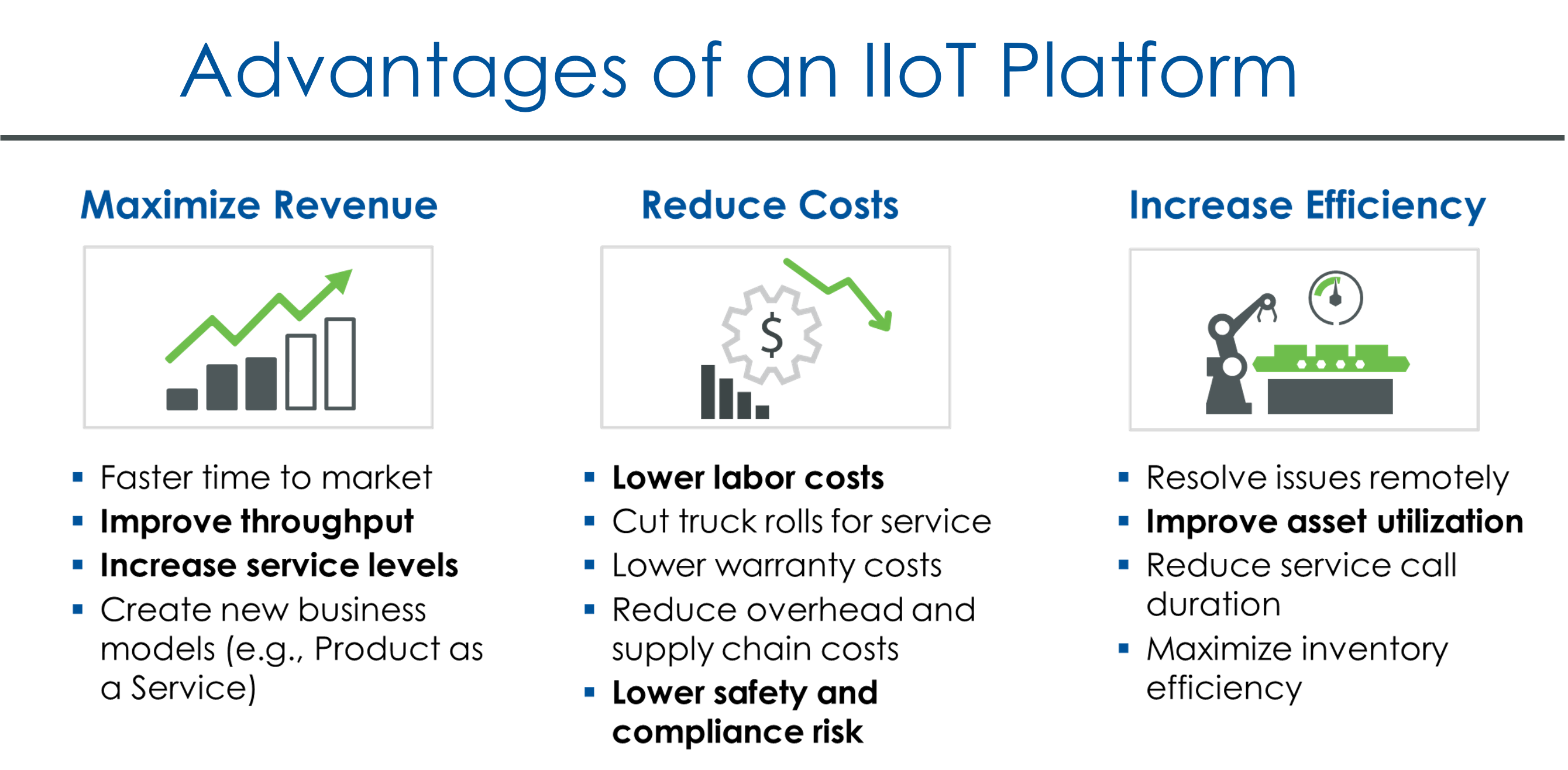
Tell us about ThingWorx and the benefits of this platform.
ThingWorx is PTC’s offering for Industrial IoT. ThingWorx contains building blocks that are pre-configured, pre-designed components that allow a user to quickly develop their applications, connectors, domain models, and user interface elements. What makes ThingWorx great is the fact that we have a digital twin, a digital representation of a real device, that goes across the environment from engineering to service to marketing and sales to product innovation to manufacturing efficiency.
ThingWorx is a leading IoT platform for manufacturing that is a purpose-build platform, built specifically for an Industrial IoT environment. The ThingWorx platform provides connectivity, scalability, and security to grow as your business grows—it can be developed, deployed, and extended quickly. The integrated platform features enable seamless development for quick and easy delivery of applications and augmented reality (AR) experiences. With the ability to be flexible and run in multiple environments, such as the cloud, on premise, or hybrid environments, ThingWorx provides and engaging experience by providing user interfaces with drag-and-drop tools that can be deployed in web and mobile applications and AR experiences.
In addition, ThingWorx can co-exist in a very vibrant ecosystem due to its compatibility with a wide range of products and services that simplify, accelerate, and enhance manufacturers’ processes and strategies.
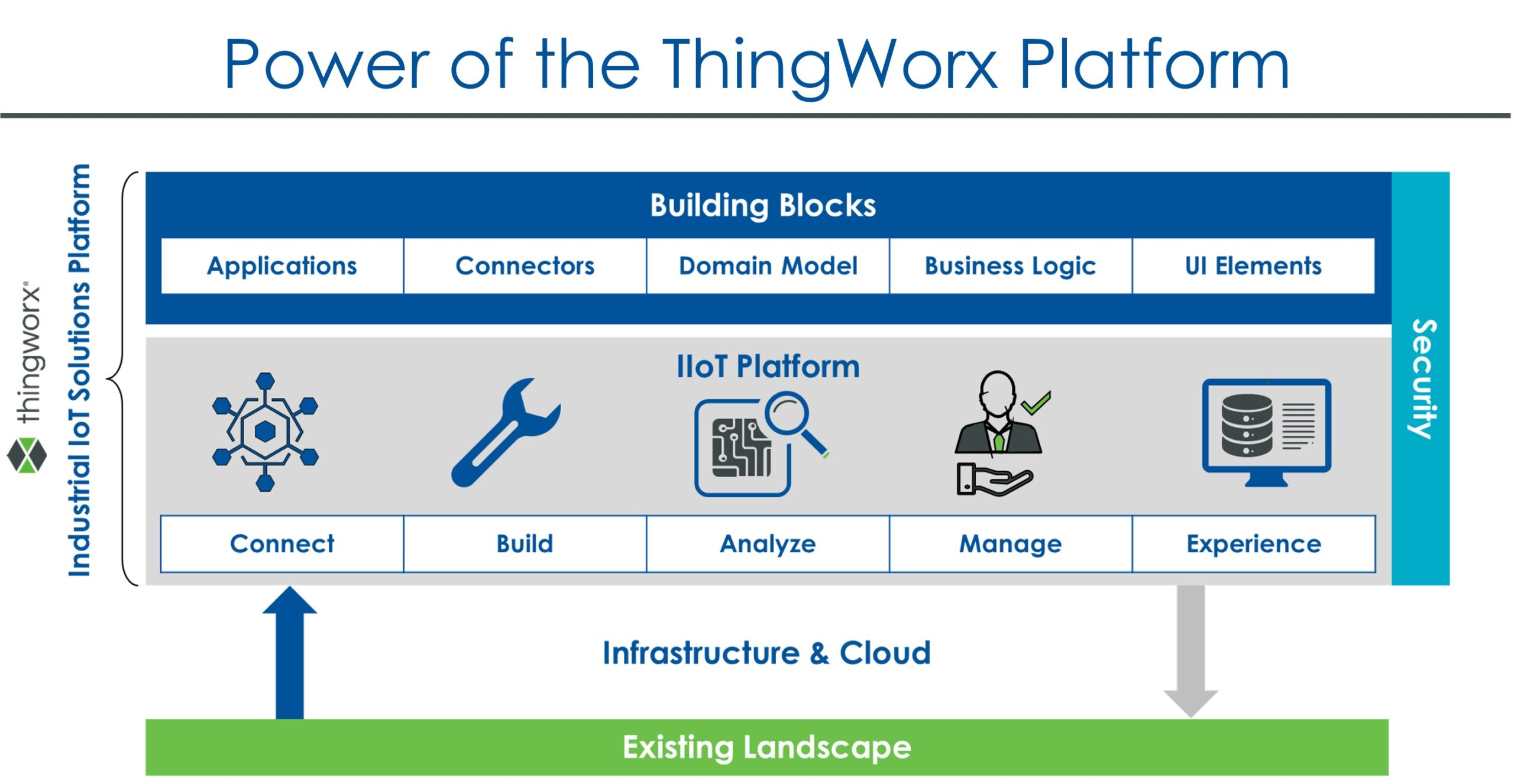
How does ThingWorx fast-track Digital Transformation?
You can build and create IoT applications quickly to fast-track digital transformation. IIoT connects all types of devices, applications, and systems for one centralized source of Industrial IoT data, and then analyzes and unlocks actionable insights into your operational data with powerful analytic capabilities. You can also manage and orchestrate connected assets, processes, and workflows. Lastly, you can provide experience by empowering your workforce with contextualized data that enhances knowledgeability, productivity, and efficiency.
Describe the technologies used to build the Paint Hangar Dashboard.
,In addition to ThingWorx, we mainly utilized Edge Microserver (EMS), which is a series of configuration files that allows us to input the IP address, as well as an application key into these files so we can connect to the right instance of ThingWorx. It also makes the connection available for the Lua Script Resource (LSR). The LSR is what we use to dynamically display the properties and simulate data. The reason we used simulated data instead of data provided by sensors is because those sensors were not available to us at the time and to keep our coding practices up to date. This practice also enables a quick deployment into an actual customer production environment.
The LSR also allows us to create our “Thing” or entity inside of ThingWorx. Once the EMS and LSR are both running correctly, that “Thing” is created inside of ThingWorx and can post property information from the LSR. For example, it can post information about the temperature and humidity, as well as other properties written to ThingWorx. By using the data inside the ThingWorx “Thing,” we can put it in context inside the ThingWorx Mashup tool. The Mashup tool is the display view where we take properties and give them context as well as add functions for user needs.
What does ThingWorx and an Industrial IoT offering provide to companies?
ThingWorx and Industrial IoT are maximizing revenue by unlocking new business models, such as product-as-a-service, to realize value-add opportunities, scale to new markets, and improve throughput. They reduce time to market with rapid application development and a vast set of capabilities to wrap and extend existing solutions. This reduces cost by leveraging data from connected products and systems to increase productivity, lower cost, and increase efficiency. They are improving quality by enhancing the quality and reliability of information to accelerate secure, scalable innovation for products, service, and factory operations. Companies can take control of their deployment with flexibility of on premise, cloud, or a hybrid approach, which is adaptable to any industrial use case.
What are the next steps?
The next step is to connect ThingWorx to Kepware Server so we can utilize the actual sensors used by the Air Force instead of using simulated code to provide data. By using Kepware, the Air Force would be able to connect many different sensors to ThingWorx and be able to view the data they want inside the dashboard. The dashboard in its current state only displays one bay of a potential seven, so creating those dashboards with more aesthetically pleasing visuals based on client needs would be among the next steps as well.
What about this do you find exciting?
As a software developer, having a tool like ThingWorx to create applications in an environment where I have access to user interface creation and styling, as well as “Thing” creation to store data, all with almost no code, is a huge help in quickly deploying applications for users. The drag-and-drop features allow you to insert widgets and tools into the user interface as well as format them to be exactly where they are needed, which also has given me a better perception and interest in design.
What is also great about the ThingWorx platform is that it allows users to have a centralized location to access their data, no matter where the data could be coming from, so users are able to access data and manage multiple devices from one location. By also being able to run analytics on the data in real time, users can reduce downtime and prevent issues from occurring even before they happen. It also is a beneficial tool for those who have a background in software programming and those who are new to it, as most of the implementation of the design is codeless.
About the Innovation Lab
Illumination Works is a leading provider of technology consulting, and as such we actively strive to stay ahead of the technology curve. We have invested in an Innovation Lab on site in our Dayton, Ohio office led by our Chief Technology Officer, Jon Mitchell and supported by our Director of Research and Innovation, Dr. Rob Keefer. They have staffed the Innovation Lab with intellectually curious and technically capable team members who work on developing and testing the latest tools and technologies.
We choose which of the newest technologies to invest in based on research and client needs and use the Innovation Lab resources to prove out relevant use cases. In addition to the current staff, the Innovation Lab is available to team members who need to do training for current assignments or improve their skills while in between assignments.
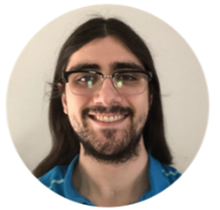
About Stefan
Stefan is an Internet of Things Digital Developer and Design for Illumination Works as part of their Innovation Lab, where he uses a suite of PTC software to create new ways to provide solutions to customer needs. He has programming experience with HTML, CSS, and JavaScript, as well as Python and C# and has been using what he knows from web design to apply his knowledge to the software suite that PTC provides, primarily ThingWorx. He has started exploring PTC’s CAD software, Creo, and Vuforia as well. In addition to the Paint Hangar Dashboard, he was also integrally involved with the user interface design and simulation code for our Micro-Model Machine Shop Simulator (smart factory), which uses both simulated and real-life data to display environmental controls, power readings, and CNC machines data. Watch for more to come on smart factory!
Click here to watch the 30-minute on-demand webinar on the paint hangar IoT monitoring.
Learn more about our AR and IoT offerings.
Reach out to Jim Blough to learn how AR and IoT can benefit your business.